Robert “Rob” Bailey president of Space
Saver Parking Company, Mid-American
Elevator Company, and USA Hoist
Company, started in elevator business in 1982 as Salesman/Project
Manager for Mid-American Elevator. Managed numerous projects including
maintenance at O’Hare Field for over 100 elevators and escalators and
$5,000,000 elevator and escalator construction contract at State of Illinois
Center in Chicago. Initiated leveraged buyout of Mid-American from previous
ownership in 1984. Assumed duties of President in 1984. Built company
business from $1,500,000 per year to approximately $30,000,000 per year.
Designed and developed microcomputer based elevator control systems starting
in 1985. Started Mid-American Elevator Equipment Company which now sells
control systems to elevator contractors all over the world.
In 1992, Mid-American opened an office in Washington DC. In a Joint
Venture with Tompkins Builders. Mid-American has performed over $75 million
of renovation work in US Government Buildings.
In 1995, Mid-American purchased the assets of USA Hoist. USA Hoist is
the largest contractor for outside construction elevators in the Midwest.
EXPO1000 - Can you give me a little
background on Space Saver Parking?
ROB - Space Saver Parking company is a leader in providing innovative
solutions to today’s complex parking problems. We started installing
stackers in 1990 and in June of this year completed our first fully
automated parking facility.
EXPO1000 - Tell me about stackers.
ROB - Stackers are your standard dependent parking platforms.
EXPO1000 - What do you mean by “dependent”?
ROB - This type of stacker requires that you have to move the
bottom car to recover the top car. This system allows for doubling
or tripling a single parking space.
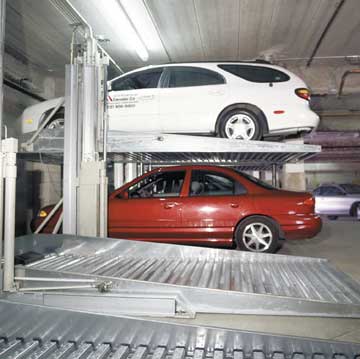
EXPO1000 - How much
will I pay to double a parking space?
ROB - If you only purchased one platform, it will cost about
$10,000 and of course as the quantity increases the price goes down.
EXPO1000 - Is there any system that
you can buy which doesn’t require moving the bottom vehicle?
ROB - Yes, we have several. If you can provide a pit of 6’,
the bottom car can go into the pit. These “independent” systems will
cost approximately $8,000 per space.
EXPO1000 - Do you have another solution
that doesn’t require the excavation of a pit?
ROB - Sure, we have a “combi-lift” which is a combination of
mechanical and an automated system. The vehicle is parked on a platform,
the driver exits, and the platform moves sideways and vertically. This
combines the advantages of vertical stacking and sideways movement to
double or triple the number of spaces in the same area.
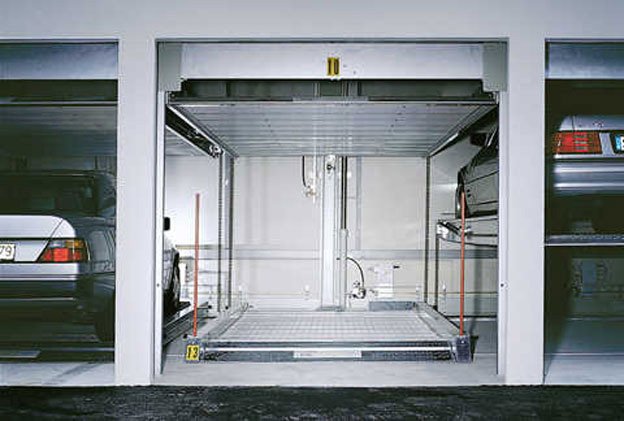
EXPO1000 - Now we’re getting into the
exciting subject of automated parking. Our parking forum in Washington
DC visited your installation at the Summit Grand Parc Apartments. We
were all impressed, surprised, and fascinated watching this demonstration.
Can you briefly describe to the unfortunate folks who didn’t see this
installation?
ROB - Summit Grand Parc is luxury residential tower with 98
rental units and 24,000 sq. ft of commercial/retail space a few blocks
from the White House on a very small footprint. This building was originally
an office building on a 60’ x 106’ lot, without any parking.
Summit Grand Parc excavated 32’ or 4 levels and we installed 74 fully
automated parking spaces.
EXPO1000 - Give me a idea of just how
the automated garage works?
ROB - A single driveway provides access to the building at street
level. Inside the building there are 2 entry/exit rooms and the vehicle
storage area is under grade.
The patron enters the building with his garage door opener.
Inside the building he drives into one of the two entry/exit rooms.
The patron drives onto a steel pallet that is flush to the floor. Channels
are provided on each side of the pallet to guide the wheels, much like
you see at a car wash.
The patron turns off the car, retrieves his belongings, passengers,
pets, and keys and vacates the transfer compartment. Outside the room
he activates the system by waving his encoded card at the card reader
adjacent to the room. The door closes, senses the size of the vehicle,
and confirms that room is unoccupied by people or pets.
The car is now resting on a pallet and the pallet is located on a turntable.
The car is ready to be automatically parked.
The turntable moves 45 degrees to line the vehicle up
with the transport device. The car is lowered by a vertical lift and
brought into the system by the SRU (Storage Retrieval Unit) that places
the pallet and car into the assigned storage rack.
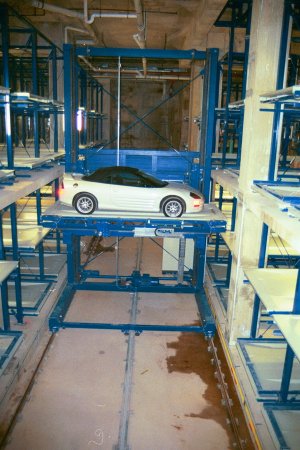
To retrieve the vehicle, the card is again read and the process starts
with the car delivered to the entry/exit area on the turntable, this
time facing the exit. The doors open and the car is ready for the owner
to drive out.
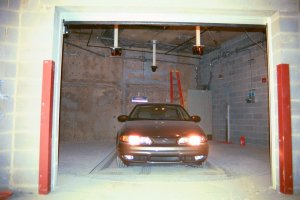
EXPO1000 - Lets talk costs. How much
did Summit Grand Parc spend for this installation?
ROB - The cost of the mechanical parking equipment without
land, excavation, and building was $1.5 million or $20,000 per space.
EXPO1000 - How does this compare to
ramp parking?
ROB - Ramp parking, in my opinion, is your most economical
alternative but if you have a small footprint or no room to build,
this is the only way to have parking spaces available - and in this
case the only viable alternative.
EXPO1000 - So what you’re saying is
that you don’t have the solution for all parking situations?
ROB - Right, but it solves many previously impossible situations.
The Summit Grand Parc project could not have been built with any other
parking solution.
EXPO1000 - Let’s talk about operating
costs. What is the annual cost of maintaining such a system?
ROB - About $400 per space per year. This includes monthly
preventative maintenance inspections and lubrication, and all required
normal repairs. It includes call back service for trouble calls
during normal working hours. It does not include repairs required
for vandalism, misuse, flood, fire, etc.
EXPO1000 - How much should be set aside
each year for capital reserves to fund future capital improvements?
ROB - The system will need a major renovation (new controls
and replacement of most heavy wear parts) in 20 to 25 years. The
cost of the renovation will be about 50% of the original purchase price
adjusted for inflation.
EXPO1000 - How many human operators
are needed to attend this system, and how many man-hours per day?
ROB - I would expect with a two hundred to three hundred car
system that you would need two persons during normal working hours and
one during nighttime hours -- approximately 32 man hours per day. This
is just operators and does not include maintenance.
EXPO1000 - What qualifications and
technical skills are required to operate and service the system?
ROB - Operators will need to be reasonably knowledgeable --
the upper end of the building engineer trade. Operators will need
to learn to operate the computer controlled diagnostic system -- so
they need to have a reasonable good level of computer literacy -- equivalent
to a proficient Internet user. Operators will need three to five
days training.
EXPO1000 - What happens when the system
fails? How quickly can it be repaired?
ROB - Usually when the system fails, it will fail in a mode
that will allow most or all of the automobiles to be accessed.
We would expect that generally a mechanic would respond in one hour
or less and that the average time to repair would be one hour or less.
EXPO1000 - What is the track record
of this system with respect to reliability?
ROB - Track record of these systems is very good in Europe.
Wohr has over 75 fully automated garages in operation with no failed
installations. Availability is over 99%.
EXPO1000 - How does someone get more
information?
ROB - For more information, call Jackie Smith at 773-486-6900
or send her e-mail at jackie@mid-americanelevator.com.
More information can be found on our web site www.SpaceSaverParking.com.
By the way, Jackie will be hosting a bus tour of the Washington DC
facility from the NPA Conference in Philadelphia on Wednesday, September
25th.
EXPO1000 - Once again, thank you for
co-hosting our event in Washington, DC and for the automated parking garage
tour.
For your information, one of our visitors
said, “This was really a historical event for the parking industry. I
felt a little like a witness on the windy sand dunes of Kitty Hawk watching
the Wright Brothers first success. Space Saver has opened a new era all
of us in the parking industry.”
ROB - Thank you very much for this opportunity and your forum.
###
|